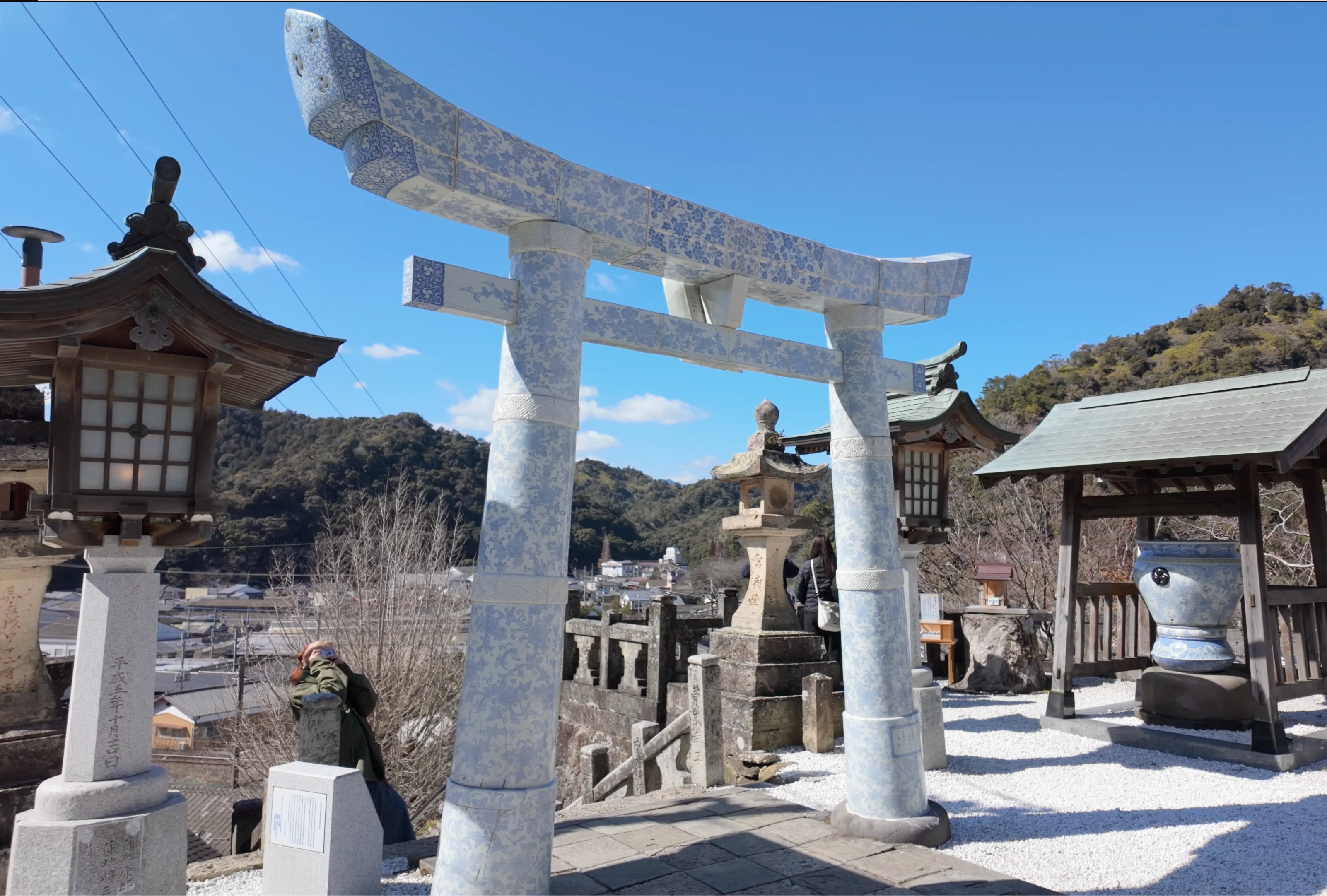
The History of Japanese Porcelain and the Story of Arita Ware
When you ask Japanese people, 'What is the most famous pottery in Japan?', most would immediately think of Arita Ware. This shows just how important Arita Ware is in Japan. Another reason for its fame is that it is the birthplace of Japanese porcelain.
What is Porcelain and How is it Different from Pottery (Earthenware)?
Pottery and porcelain differ not only in their raw materials and firing temperatures but also in their firing methods. Porcelain requires a much higher kiln temperature than pottery. Pottery is primarily made from clay and typically undergoes oxidation firing, which involves ample airflow. In contrast, porcelain is made from kaolin and fired in a low-oxygen environment through reduction firing.
As a result, pottery is usually opaque, earth-toned, and emits a dull sound when struck, while porcelain appears translucent white and produces a clear, bell-like tone. The iron in pottery's raw materials oxidizes during firing, giving it reddish hues. Porcelain, on the other hand, often displays bluish celadon tones or its signature white, thanks to the effects of reduction firing.
How Japan Started the Production of Porcelain
Porcelain is a type of pottery that has been fired in China since ancient times. It requires a mineral called kaolin and cannot be produced without high-temperature firing. Unlike regular pottery, porcelain does not absorb water.
Until the Azuchi-Momoyama period (1573–1603), Japan lacked the technology to fire porcelain and could only produce unglazed pottery. At that time, pure white porcelain that shone like jade, as well as vividly dyed pieces using gosu (a cobalt-based pigment), were highly prized by Japanese aristocrats as imported goods. In addition, ceramics used in tea ceremonies were mainly imported from Korea.
Daimyo and samurai of the time were drawn not only to the political importance of the tea ceremony as a means of forging alliances, but also to its aesthetic refinement. They collected tea utensils, often seeking rare and valuable items to display their wealth and status. A famous example is Katagiri Sekishū, who designed Jikōin Temple as a tea ceremony space and became a tea master himself.
It was not until Hideyoshi's military campaigns in Korea that Japan began producing porcelain domestically. After the invasion, several daimyos brought Korean potters back to Japan and tasked them with producing and teaching pottery. Nabeshima Naoshige, the feudal lord of Hizen Province, brought back a Korean potter named Yi Sam-pyeong (李参平, known in Japan as Resampe). Yi spent 12 years searching for kaolin in Hizen Province and eventually discovered high-quality deposits in Izumiyama, Arita. After six more years of work, he succeeded in producing the first porcelain in Japan.
Today, Yi Sam-pyeong is honored as the founder of Japanese porcelain at the Sueyama Shrine in Arita Town.
Following this success, the Nabeshima clan established the Sarayama Daikansho to oversee porcelain production and manage the craftsmen in Arita, making it the sole producer of porcelain in Japan at the time.
Industrialisation of Ceramic and Gottfried Wagener
In Meiji Era, a German chemist named Gottfried Wagener had changed the whole ceramics industry in Japan. In short, if Wagener didn’t go to Japan or work for the Wald Trading Company, the ceramics industry might not have developed in the same way as it has done.
He was hired by the Wald Trading Company for quality inspection by using knowledge of physics and chemistry when the company exporting porcelain from Nagasaki Trading company. As he learned more about Arita porcelain, Wagener became more and more fascinated with it; and he showed porcelain experts in Arita in his laboratory in Nagasaki how to dissolve gold in aqua regia (a liquid mixture of 3 parts nitric acid to 1 part hydrochloric acid) and a method to use coal as fuel instead of firewood and charcoal.
Later, he got permission to visit the production centre in Arita which had to be approved by the lord of Saga domain, Nabeshima Naomasa. Luckily, Saga domain was encouraging new industries at that time and needed such person with advanced knowledge of physics and chemistry. There was nobody who had the skill to reproduce the colours of the European porcelain.
During his time in Arita, he made three major achievements: 1) the use of cobalt pigment; 2) the study of glaze; and 3) the development of coal kilns.
Firstly, the gosu pigment (cobalt pigment) was imported from China to produce sometsuke (blue and white) porcelain. Wagener managed to reduce the cost significantly by using industrially manufactured cobalt pigment. In addition, he tried to produce porcelain by using a coal kiln, which is more suitable for mass production as it cost less than using firewood or charcoal. In 1637, to prevent the overcutting of trees, the Saga domain ordered the chief retainer Taku Mimasaka-no-kami to evict Japanese potters and forced them to reduce the production of pottery. Obviously, government polices didn’t solve the fundamental problem of production of porcelain. The experiment of firing potteries using Wagener’s prototype coal kiln was not successful on this occasion; however, Wagener’s experiment methods and inquisitive scientific spirit were passed down. In 1909, about 40 years after Wagener’s first visit, Fukagawa Eizaemon and others, who were influenced by Wagener, constructed a full-fledged coal kiln in the factory of Korasha. It saved more than 30% of the fuel costs, and it was extremely useful for the manufacturing of insulators, which are used as parts for electric cables.
Moreover, Wagener stood apart from most of the foreign experts hired by the Meiji government. He deeply appreciated the artistic excellence of traditional Japanese crafts and believed it could serve as the foundation for Japan’s industrial strength—something Western nations could not imitate. He warned that merely producing cheap, uniform goods would not be sustainable, as Japan would eventually be outcompeted by Western firms with greater capital and more advanced facilities. Instead, he argued that Japan should refine and leverage its artistic heritage to appeal to global audiences, regardless of cultural or civilizational differences. Wagener also appeared to believe that this distinctive artistic quality stemmed from a refined aesthetic sensibility shaped by Japan’s traditions and way of life. Thus, he emphasized the importance of respecting and preserving Japanese identity to further enhance Japan’s uniqueness.
Amid the major political and social changes from the Edo to Meiji periods, Arita porcelain risked becoming outdated. However, influenced by Wagener’s teachings, Arita evolved into a competitive industry. Its history of incorporating techniques and aesthetics from Korea, China, and Europe laid the groundwork for modernization. As Arita porcelain marks its 400th anniversary, there is hope for future innovation that balances traditional Japanese aesthetics with scientific inquiry, following Wagener’s example.
The export of Arita Porcelain
In the 1640s, Jingdezhen's famous gosu blue-and-white porcelain, known for its thin and refined form, represented the most advanced porcelain-making techniques of the time and was the largest export product in the world. However, in 1655, when the Qing Dynasty imposed a maritime ban that restricted exports, European orders shifted to Arita in Japan.
By the 1660s, Sakaida Kakiemon had developed the Kakiemon-style overglaze porcelain and became one of the first in Japan to master the art of enamel decoration. Kakiemon’s works featured vibrant colors and a unique aesthetic not found in Jingdezhen’s blue-and-white porcelain. They sparked a major boom in Europe and went on to significantly influence Meissen porcelain in Germany, as well as eventually rivaling Jingdezhen itself.
As we’ve explored, Arita’s porcelain industry emerged from centuries of cultural exchange, technical innovation, and artistic refinement—from Korean pottery traditions to European influence, and from the discovery of kaolin to Wagener’s modernizing efforts in the Meiji era. These foundational developments not only shaped the identity of Japanese porcelain but also positioned Arita as a global force in ceramic artistry.
In the next post, we’ll follow the remarkable journey of Arita porcelain beyond Japan’s shores—how international trade, shifting political tides, and the creativity of pioneers like Sakaida Kakiemon propelled Arita onto the world stage. Discover how Arita’s distinctive aesthetic captured European imaginations and left a lasting imprint on global porcelain history.